How Group Training is Closing the Skills Gap in Manufacturing
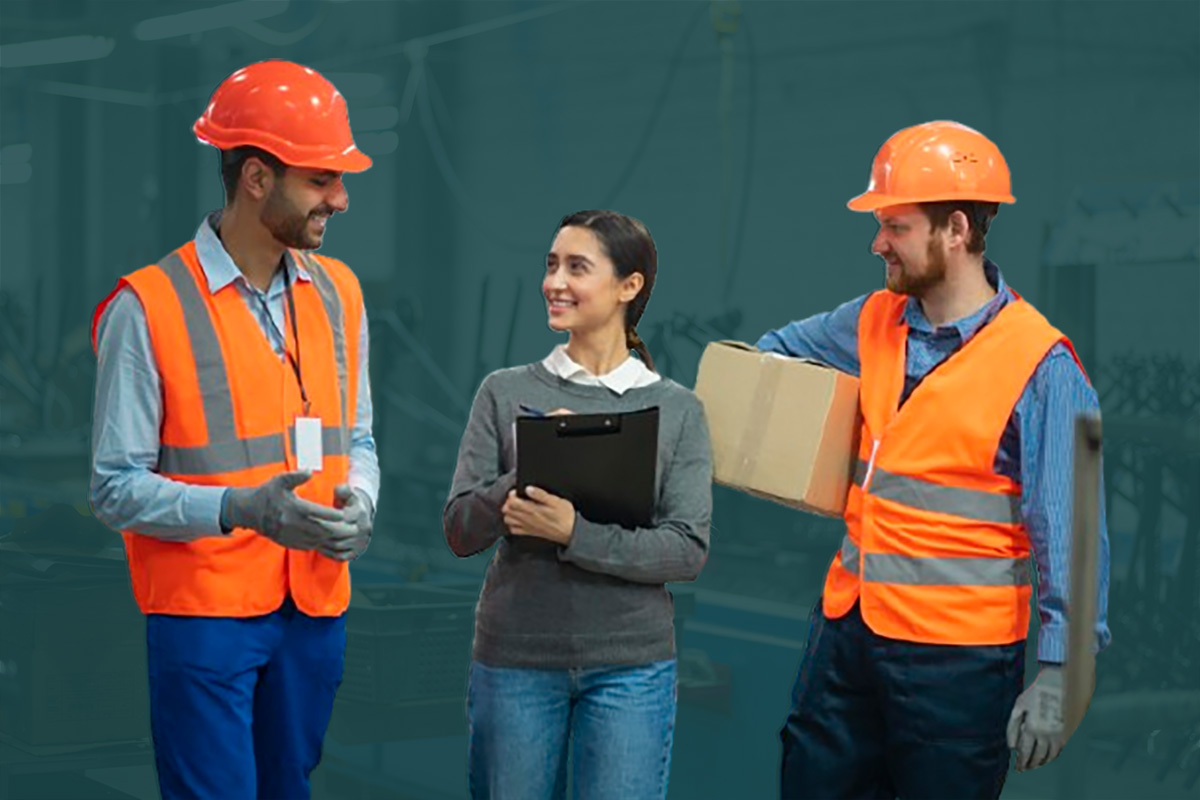
Manufacturing is one of the cornerstones of any economy, and Australia's is no exception. Yet, despite the industry’s importance, there is a growing concern about the skills gap in manufacturing. With an aging workforce and fewer young people entering the trade workforce, the challenge of closing this gap has never been more pressing. Enter group training in manufacturing—a game-changer for both employers and employees. But how exactly is it helping? Let us break it down for you.
The Skills Gap: A Growing Concern in Manufacturing
Australia's manufacturing industry is facing a shortage of skilled workers. The demand for specialized skills, like machinery operation, welding, and maintenance, is outpacing the number of qualified workers entering the field. This skills gap is particularly noticeable in small and medium-sized enterprises (SMEs) who struggle to find workers with the right training and experience.
The problem is not just about filling positions; it is about finding employees with the right manufacturing skills to keep up with technological advancements and industry demands. A growing number of positions in manufacturing require workers to be skilled in a mix of traditional trade skills and modern technologies. This shift has made it more difficult for the current workforce to keep up, leading to increased pressure on employers to find solutions.
Why Group Training in Manufacturing Works
Group training has emerged as an effective solution to address the skills gap. It involves a structured approach where employees from various organizations are trained together, sharing the learning experience and knowledge. This model allows companies to upskill their workforce without having to individually train each employee.
Cost-Effective and Accessible
For small and medium-sized enterprises (SMEs), group training offers an affordable way to train multiple employees at once. Rather than spending large amounts of money on individual training programs, companies can pool their resources, offering employees a quality education without breaking the bank.
Hands-On Learning
One of the most valuable aspects of group training is the focus on hands-on experience. Participants can learn how to operate equipment, fix machinery, and apply manufacturing skills in real-world scenarios. These practical exercises not only teach technical skills but also improve problem-solving and critical thinking. Workers leave these training sessions ready to perform their tasks on the job.
Improved Workforce Collaboration
Group training also promotes teamwork. Employees from different companies get to work together, sharing knowledge and experiences. This collaborative environment not only helps build strong professional relationships but also encourages the exchange of ideas and best practices. This is especially important in manufacturing, where teamwork can make or break the success of a project.
Filling the Trade Workforce Gap
Group training offers a unique opportunity to bridge the trade workforce gap. As the older generation of workers prepares for retirement, younger workers entering the field need to be quickly trained. Group training allows new workers to enter the manufacturing industry with the skills they need to succeed, helping reduce the impact of the aging workforce.
How Group Training Benefits Employers
Employers in the manufacturing sector face a constant challenge in maintaining a skilled workforce. By offering group training programs, employers can ensure their employees are well-prepared for the demands of the industry. Here are just a few of the key benefits:
Increased Employee Retention
Investing in group training helps employees feel valued, which in turn leads to greater job satisfaction and loyalty. When employees are given the opportunity to develop new skills, they are more likely to stay with a company long-term. This reduces turnover rates and the associated costs of hiring and training new employees.
Better Productivity
A well-trained workforce is a productive workforce. When employees are trained through group training programs, they gain the knowledge and confidence to perform their roles more effectively. This leads to faster production times, fewer mistakes, and ultimately better-quality products.
Flexibility in Training
Manufacturers are often facing changing demands and technologies. Group training provides flexibility to quickly update workers' skills to keep pace with new developments. Training programs can be customized to meet specific industry needs, allowing businesses to stay competitive in a fast-evolving marketplace.
The Future of Group Training in Manufacturing
As the skills gap continues to grow, group training will play an even more important role in shaping the future of the manufacturing industry. Employers will need to embrace these training models to stay competitive and ensure they have a workforce that is prepared for the challenges ahead.
The future of manufacturing in Australia depends on having a skilled workforce that can adapt to new technologies and evolving industry needs. Group training provides an effective solution that benefits both employees and employers. By investing in group training, you are not only closing the skills gap but also securing the future of your business and the broader manufacturing sector.
Conclusion: Closing the Skills Gap, One Group at a Time
In a world where technological advancements are reshaping the landscape of manufacturing, group training is a key player in closing the skills gap. It provides an affordable, hands-on, and collaborative approach to training workers, helping them acquire the necessary skills to thrive in the industry. As the trade workforce continues to evolve, group training will be the bridge that connects the old guard of manufacturing expertise with the new generation of skilled workers.
If you are in the manufacturing industry, consider incorporating group training into your workforce development strategy. It may just be the solution you need to close the skills gap and drive your business forward.